In the world of industrial manufacturing, precision and efficiency are of utmost importance. To achieve this, companies need to invest in cutting-edge technology that enhances their production processes. One such technology that has revolutionized the manufacturing industry is the Horizontal Machining Center (HMC).
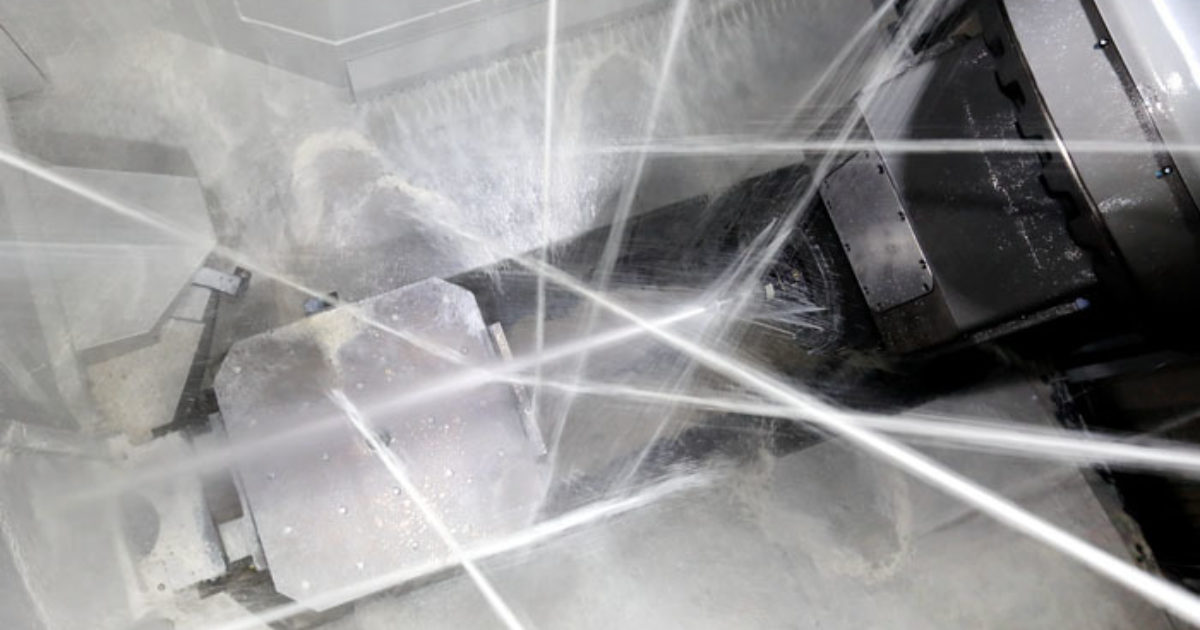
A Horizontal Machining Center is a machine tool that is used for milling, drilling, and tapping of complex parts. It works by using a rotating spindle that horizontally moves across the workpiece. The workpiece rests on a pallet and is moved on the pallet changer, which enables the machine to process multiple workpieces simultaneously. By enabling multi-axis machining, HMCs can perform a wide range of tasks, including CNC routing, turning, boring, and more.
The horizontal orientation of the spindle in an HMC allows for increased stability and improved tool accessibility. This means that HMCs can operate at higher speeds and with greater precision than other types of machining centers. This makes horizontal machining more accurate, dynamic and efficient while removing the limits on the machines operating envelope, thus allowing components which are taller and larger in size to be effortlessly machined.
Advantages of Horizontal Machining Centers
1. Decreased Set-Up Time: HMCs feature pallet changers which drastically decrease set-up and down-time. This feature allows the operator to switch between parts seamlessly, therefore, reducing delays during workpiece changes.
2. Multi-Sided Machining: One of the unique capabilities of HMCs is its multi-axis machining ability. This feature allows the machine to easily process complex parts that require high accuracy and precise detail.
3. Enhanced Surface Finish: HMCs are specially designed to produce a superior surface finish with a high level of accuracy. The horizontal spindle orientation enables faster, more efficient material removal, thereby reducing the need for finishing operations.
4. Cost-Effective: HMCs offer a more efficient and cost-effective way of producing complex components compared to traditional methods such as manual milling techniques or multi-stage CNC machining operations.
Applications of Horizontal Machining Centers
HMCs have a wide range of applications in the manufacturing industry, making them popular among engineers, machine operators, and designers. Some of the popular applications of HMCs include:
1. Aerospace: HMCs are widely used to produce parts used in the aerospace industry. This is because the industry demands components that are lightweight, durable and precise with tight tolerances.
2. Automotive: HMCs are commonly used for manufacturing various parts, such as gearboxes, engine components, chassis parts and more.
3. Medical Devices: HMCs are essential in the manufacturing of complex medical instruments and machinery components such as implants, surgical devices, and pacemakers.
4. Machinery: The machining of large and bulky machinery components is an area where HMCs excel due to their large work areas and ability to carry heavy loads.
Conclusion
With innovation being the cornerstone of modern technology, Horizontal Machining Centers are essential for modern manufacturing. They provide a versatile, stable and efficient machining solution for companies that require high precision, reduced cycle times and quality parts. The use of HMCs not only increases productivity but also improves the quality of finished products, reduces operating costs and meets the demands of the customers. Therefore, if you are looking to improve your production processes, investing in HMCs will be a wise decision.